Sealed Pneumatic Actuator (Single Acting)
Unsealed Pneumatic Actuator (Single Acting)
Unsealed Pneumatic Actuator (Double Acting)
Focusing in continuous improvement
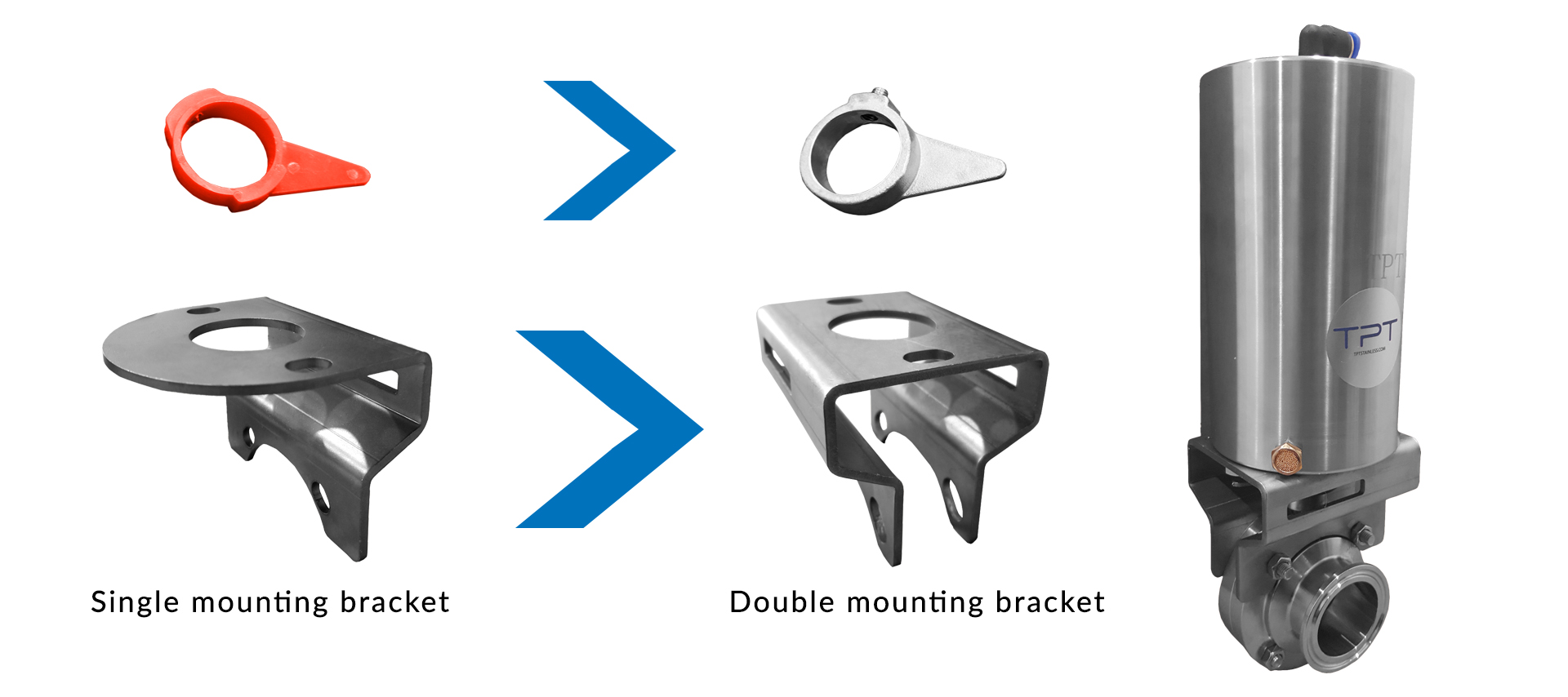
Unlike other designs that produce an off-axis thrust, our redesigned mounting bracket minimizes the shaft side loading, putting less stress on seals resulting in less wear.
Sealed Vs Unsealed Actuators
Sealed actuator
Sealed actuators are maintenance free. (Repair kit unavailable)
Unsealed actuator
Available for preventive/corrective maintenance.
Life service of a pneumatic actuator is significantly extended only with a grease re-lubrication and replacement the O-ring seals (Repair kit available)
How do I choose the right actuator for my application?
It depends on the number of operation cycles. For example, some actuators may perform hundreds of cycles per hour, whereas others open and close just once a day.
Please take a look at the chart below to make a decision.
Cycles rate | Cycles per hour | Actuator recommended |
---|---|---|
Low | 1 to 5 | Sealed |
Medium | 6 to 19 | Sealed / Unsealed |
High | 20 to 30 | Unsealed |
Note: TPT pneumatic actuators are factory-lubricated for life to ensure a trouble-free service life and 1,000,000 cycles may be expected. However, this applies under ideal conditions. Under real conditions, the service life depends on several factors.
Contaminated air from air compressors and air supply system is the most common cause for shortened life service (solids, water, and oil). This contamination will gradually degrade and wash out the original grease lubricant. This will shorten the service life, therefore it will be almost impossible to accurately predict the service life.
If the compressed air supply is clean, dry and filtered to 40 micron, the grease will give the seals and components long life without adding oil through an oil mist lubricator.
The oil mist lubrication will extend the life of the actuator, but it will also wash out the original lubrication. Once begun, the oil mist lubrication cannot be discontinued and the lubricator should be regularly checked and maintained. If air lubricators are used, the lubricant selected must be compatible with Nitrile (Buna-N) seals.
Pneumatic actuator operation principle
Single acting pneumatic actuator
To open the valve : Air pressure is applied to port A, this causes the piston to drive the shaft in a quarter turn rotation forcing to compress the spring and exhaust the air through port B.
To close the valve: When the air pressure is relieved, the spring force moves the piston to drive the shaft in a quarter turn rotation and exhaust the air through port A .
The single acting actuator is normally controlled by a 3/2 directional valve (soleniod valve)
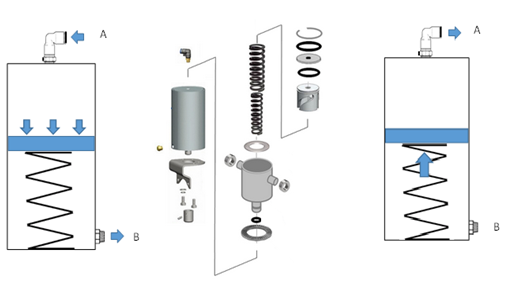
Why the single acting actuator is the most popular in the food and beverage industry?
The advantage of choosing the spring return actuator over the double acting actuator is predominantly for safety reasons.
Is important to safe guard the process when the power or electrical signal failure. When this happen, the spring drives the valve to a predetermined safe position.
The spring return actuator can be set up for fail with the valve closed or with the valve open.
We can configure your valve for fail position upon request.
Double acting pneumatic actuator
To open the valve : Air pressure is applied to port A, this causes the piston to drive the shaft in a quarter turn rotation and exhaust the air through port B.
To close the valve: Air pressure is applied to port B, this causes the piston to drive the shaft in a quarter turn rotation and exhaust the air through port A.
Power or signal failure in a double acting actuator leaves the valve in its last position.
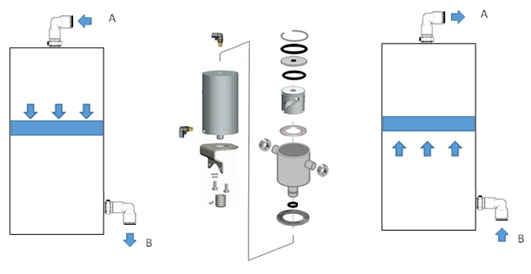